精密火花机定制
镜面火花机放电的主要参数有放电电流,电流越大,表面粗糙度越差。放电电流大小的选择和电极的表面投影面积,放电间隙有关。放电间隙。一般来说,单轴火花机的放电间隙会比数控火花机或镜面火花机的小,因为单轴火花机/ZNC火花机没有摇动,三轴联动数控火花机也叫镜面火花机是要摇动。这是需要特别注意的地方。放电时间。放电时间越长,加工效率理论上越高,但要注意的是容易产生积碳或拉弧的现象。排渣时间。一般叫脉冲间隔,它是和脉冲宽度搭配使用的,不同品牌的火花机搭配不太一样,具体需要详见所使用厂家火花机的说明书。电压。有些品牌的数控火花机会有高压、低压的选择。通常情况下,电流大的时候用低压,电流小的时候比如1A的时候可以考虑加高压。其他参数。放电异常检测,在放电状态不好的时候可以调节。火花机利用火花放电时产生的腐蚀现象对材料进行尺寸加工。精密火花机定制
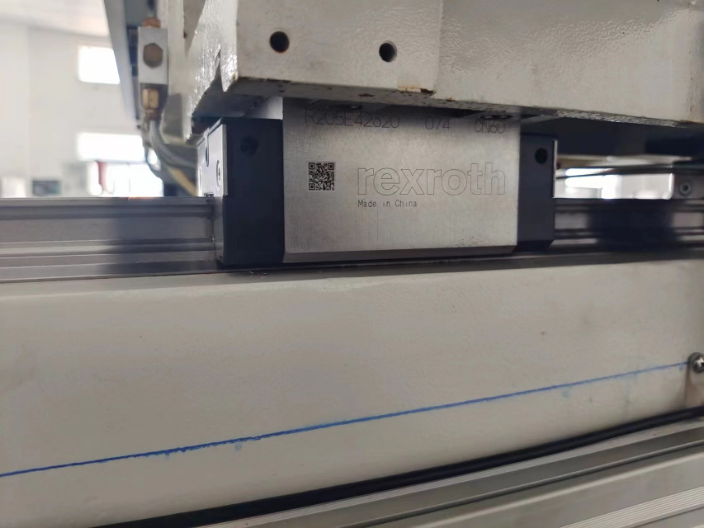
选择适合的火花机型号需要考虑工件的材料和形状。首先,材料的硬度是选择火花机的关键因素之一。对于硬度较低的材料,如铝合金或塑料,可以选择低功率的火花机,以避免过度烧损。而对于硬度较高的材料,如钢或铸铁,需要选择高功率的火花机以确保足够的切削能力。其次,工件的形状也会影响火花机的选择。对于较大和复杂形状的工件,需要选择具有较大工作台和多轴控制功能的火花机,以便进行精确的加工。而对于较小和简单形状的工件,可以选择较小的火花机,以提高加工效率。除了材料和形状,还应考虑其他因素,如加工精度要求、加工速度、设备价格和维护成本等。可以咨询专业的火花机制造商或经验丰富的操作人员,以获取更详细的建议和指导。具体选择应该是综合考虑以上因素,并根据具体需求做出合理的决策。深圳工业火花机费用火花机加工过程便能日以赴继地自动运转。
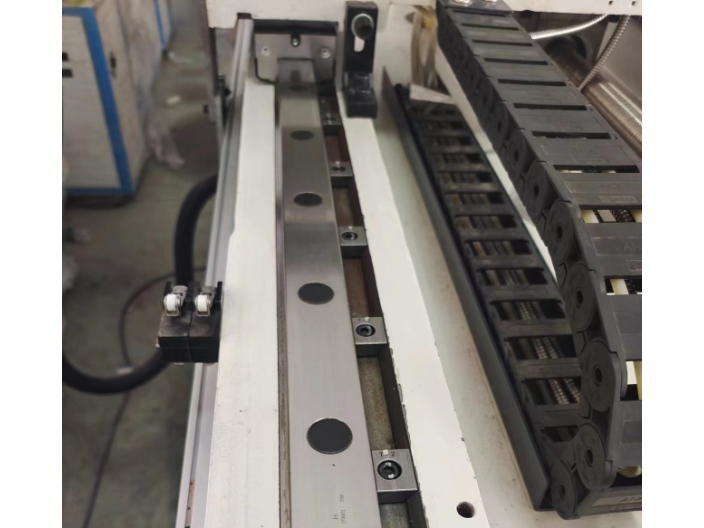
当前,通过检测放电位置,研究放电点的分布情况,进而预测放电状态,这是一种主动的控制手段,即在不利于电火花稳定加工因素出现前,主动地调节各个参数,从而减少不利因素的发生,保持稳定的放电加工,从而提高电火花加工速度和加工质量。目前,主要应用的检测方法有声波信号检测法、分割电极法、分割电流法、电位差法和霍尔元件法。为了实现稳定的电火花加工,就需要减少放电点集中造成的电弧放电现象,使放电点能均匀地分布在加工表面。对放电状态的检测与判断虽能对稳定的电火花加工起到促进作用,但这种方法是一种被动的调节手段,即只有在发生了不利于电火花放电加工的状态后,再去进行调节,因此这种检测调节方法总是滞后加工状态,从而影响了加工质量和加工速度。
选择合适的冷却液是提高火花机加工效率的关键。以下是选择冷却液的几个要点:1.温度控制:冷却液应具有良好的热传导性能,能够快速吸收和散发热量,保持工件和刀具的适宜温度。选择具有较高的热传导系数和热容量的冷却液,可以提高加工效率。2.润滑性能:冷却液应具有良好的润滑性能,能够减少切削力和磨损,延长刀具寿命。选择具有较低的摩擦系数和较高的润滑性能的冷却液,可以提高加工效率。3.防锈性能:冷却液应具有良好的防锈性能,能够防止工件和刀具的生锈和腐蚀。选择具有较高的防锈性能的冷却液,可以提高加工效率。4.环保性能:冷却液应具有较低的挥发性和毒性,对环境和人体健康无害。选择符合环保标准的冷却液,可以提高加工效率。综上所述,选择具有良好的热传导性能、润滑性能、防锈性能和环保性能的冷却液,可以提高火花机的加工效率。在选择时,可以参考产品说明书、生产厂家的建议和其他用户的评价。火花机用于小孔加工、刻英表面合金化、表面强化等其他种类的加工。

脉冲电压在两电极相对接近的另一点处击穿,产生火花放电。这样,虽然每个脉冲放电蚀除的金属量极少,但因每秒有成千上万次脉冲放电作用,就能蚀除较多的金属,具有一定的生产率。在保持工具电极与工件之间恒定放电间隙的条件下,一边蚀除工件金属,一边使工具电极不断地向工件进给,然后便加工出与工具电极形状相对应的形状来。因此,只要改变工具电极的形状和工具电极与工件之间的相对运动方式,就能加工出各种复杂的型面。工具电极常用导电性良好、熔点较高、易加工的耐电蚀材料,如铜、石墨、铜钨合金和钼等。在加工过程中,工具电极也有损耗,但小于工件金属的蚀除量,甚至接近于无损耗。火花机每个脉冲放电蚀除的金属量极少。精密火花机定制
火花机通道能量的作用,可使电极局部被腐蚀。精密火花机定制
主板本身有故障可能是由于主板本身的组件,主机启动后可能无法通过BIOS自检。部分IDE和FDD接口出现故障,导致系统读写出现问题。火花机床的主机短则三到五天,长则三到四个月死机。这是较难确认原因的一类问题。当主板单独测试或不在用户环境中测试时,主板不会死机。这种问题关系到用户系统,甚至关系到系统的现场布局和抗干扰能力。如果遇到这样的问题时,不要盲目的把责任归咎到工业电脑上,而是引导用户从周边环境去解决问题。有些故障可能是由不同的用户程序引起的。当火花机死机时,要冷静发现分析,然后解决问题。精密火花机定制
上一篇: 湖北镜面火花机厂家
下一篇: 大型数控铣床价格多少