连云港小孔穿孔机公司
穿孔放电打孔打不下去,旋转头来回往复频繁,原因主要有以下几方面:工件装夹不好,高频采样不同步,建议小工件放置在采样工作台上,一定要用胶水或者压板将工件固定好;脉宽,脉间,脉高等参数设置有误,厚度较大的工件可适当调高脉宽和脉高值,否则下穿到1/2高度以后,放电量不够则旋转头来回往复。工件表面有氧化层,与工作台的接触不好,高频正是连在工作台上面的,这样情况孔打不下去,主轴旋转头会往冲,压弯铜管。调整一下工件位置,或磨一下工件表面去掉氧化层。数控穿孔机控制系统是一套集加工孔位编辑和小孔加工于一体的控制系统;连云港小孔穿孔机公司

大家都知道像数控穿孔机这种大型机械是由比较多个小零件组成的,这些零件缺一不可,尤其像电极铜管这种比较重要的零部件,一旦安装有一点偏差,就会给数控穿孔机机床带来比较严重损失。接下来,为大家讲解下数控穿孔机在更换电极铜管时有哪些需要注意的事项?数控穿孔机在安装电极铜管时应小心避免电极铜管被弯曲,再将铜管电极套上对应尺寸的橡胶止水密封圈,使铜管电极伸出止水密封圈2~3毫米距离,,将铜管电极套入,由铜管电极夹头本体上方插入电极夹头,将橡胶止水密封圈套紧于电极夹头上,将电极夹头本体装于主轴并旋紧(勿太紧)。此时应确实检查铜管是否在夹头中间。一切准备完毕就可开始加工。其实在数控穿孔机上安装电极铜管说简单也是简单,只要严格按照标准来操作,就可以了。宿迁高速穿孔机机床价钱苏州泰兰特进出口贸易有限公司技术力量雄厚,工装设备和检测仪器齐备,检验与实验手段完善。
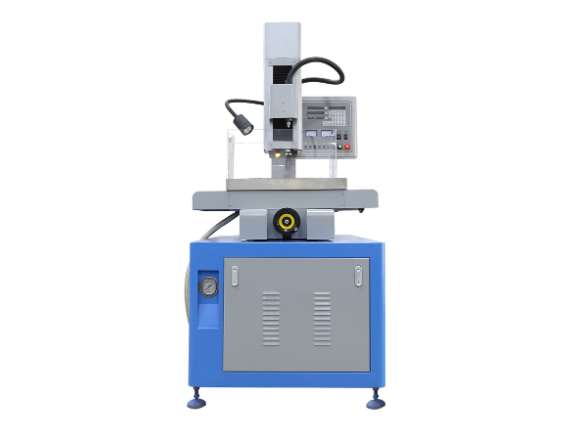
数控穿孔机一般故障的处理:1、如果数控穿孔机的旋转头不转该怎么办呢?我们首先要检查接插件是否接触不良,再调节旋转头电机的固定螺丝,如果按钮坏了,要及时更换,操作箱内部的继电器损坏也要及时更换。2、当数显表不显示或者显示不准的时候,要检查数显表上的保险丝是否断开,如果断了,请及时更换,还有光尺也有可能故障。3、当加工时短路频繁,主轴速度进给速度太快,我们要注意的是①伺服旋钮调节不当,间隙电压压得太低。②工作液泵停止工作或电极管堵塞,造成电极管中间没有冲液。③主轴伺服板(HM6-2006)有故障。细电极加工时速度比较慢时,我们要检查是不是脉冲参数选择不合理,伺服旋钮是否调节不当;查看电极是否有不直、弯曲的问题,或者电极材料的质量是否有问题。5、当细电极加工烧电极时,检查电源板是否有故障,交流接触器是否损坏,还有按钮也可能坏了。
主传动的方式及特点?穿孔机的主传动电机可以使用直流电机或交流电机。直流电机一般通过传动轴直接与轧辊连接,而交流电机则通过减速机和传动轴与轧辊连接。一个机组可以使用一个电机,即一个电机连接减速机,减速机输出两个输出轴用来驱动轧辊。也可以每个轧辊使用一个电机单独驱动。穿孔机使用的接轴有万向接轴和十字头接轴。十字头接轴具有良好的调节性能,无论在水平面和垂直平面内都可以产生相对的角位移。穿孔机传动轴与轧辊的连接方式?主要连接方式有两种.一种是螺栓连接,这种方式普遍使用,不足之处是拆卸时间较长且在生产中容易松动.两一种方式是扁轴连接,拆卸十分容易,越来越多被采用.数控穿孔机的特点:低损耗。

数控穿孔机加工过程中的极性效应是什么?当正负电极表面受到负电极和正离子的轰击和瞬时热源的作用时,在两极表面分配到的能量不一样,所以熔化。当汽化抛出的电蚀量液不一样时,电子的质量和惯性就比较小,比较容易获得比较的速度和加速度。在击穿放电的初始阶段只有小部分正离子由于质量和惯性较大,容易获得比较的速度和加速度,在击穿放电的初始阶段就有大量的电子奔向电极,把能量传递给正极表面,使正极材料迅速熔化和汽化,而正离子由于质量和惯性大,启动和加速较慢,在击穿放电的初始阶段只有少部分的正离子来得及到达负极表面并传递能量。选择加工极性,在用短脉冲加工时,质量和惯性大的正离子将有足够的时间的加速,到达并轰击负极表面,由于正离子的质量大,对负极表面的轰击破坏力强,采用长脉冲时负极的蚀出速度要比正,这时工件接负极。数控穿孔机加工石墨有什么好处:石墨容易破碎,制作时要特别小心,尤其是转角的地方,不能用酸性溶液蚀刻。连云港小孔穿孔机公司
数控穿孔机可加工孔径0.3-3.0mm,深径比达300:1以上。连云港小孔穿孔机公司
数控穿孔机控制措施:工作中1.操作员应站在绝缘橡胶或木质踏板上。2.请勿用手触摸电极。3.在装卸工件,定位,校正电极和擦拭机床时,必须切断脉冲电源。4.工作液位应保持在比工件表面高50-60mm的高度,以免在液位太低时起火。5.及时清理分解的有害气体。6.严禁一个人同时操作两个以上的机床。在操作过程中不允许离开工作位置。如果需要离开,必须停止机器。工作结束:在工作结束时,必须切断电源,必须清理机器上的碎屑,油渍和现场卫生设施,并且必须清理工作现场。填写设备运行记录和班次记录。连云港小孔穿孔机公司
上一篇: 宿迁定制快走丝线切割价格
下一篇: 台州多次快走丝线切割机床